From our earliest primitive tools to our first attempts at flight, we’ve been searching for materials that are both light and strong. Especially in the design of automobiles, aviation and other products, considering the needs of safety and reliability, metal materials are undoubtedly recognized as the first choice, but the weight of steel undoubtedly makes designers feel distressed. So, is there a metal that can meet the requirements? What about people’s demand for lightweight design? Magnesium is the best choice.
Magnesium (Mg), the eighth most abundant element in the Earth’s crust, is 33% lighter than aluminum, 60% lighter than titanium, and 75% lighter than steel. Magnesium alloys composed of other elements also have outstanding advantages such as low density, high specific strength, large elastic modulus, good thermal conductivity and shock absorption, strong electromagnetic shielding performance, good biocompatibility, and easy recycling. 21st Century Green Structural Materials” has also been advertised by many industry experts as one of the star materials in the future metal industry.
Classification of Magnesium Alloys
Magnesium alloys are mainly divided into wrought magnesium alloys and cast magnesium alloys.
Deformed magnesium alloys are suitable for plastic forming. In plastic deformation, magnesium alloys still maintain the characteristics of pure magnesium. Most deformed magnesium alloys are plastically formed in a hot state, and semi-finished products such as plates, rods, shapes, tubes, wires and forgings are made by rolling, extrusion, forging, drawing and other processes. Wrought magnesium alloys are usually classified according to their chemical composition: ①Mg-Mn series: mainly used in the manufacture of aircraft skins, wall panels, and die forgings with complex shapes and parts requiring high corrosion resistance in gasoline systems; ②Mg-Al-Zn series : used to manufacture complex forgings and die forgings, missiles, etc.; ③Mg-Zn-Zr series: mainly used for the production of extrusion products and forgings for aircraft internal parts, ④Mg-Th series: used for working temperatures below 350 parts.
Cast magnesium alloys are suitable for filling molds in a molten state to obtain blanks that are close to the shape and size of the final use. Cast magnesium alloys can be divided into general cast magnesium alloys, high-strength cast magnesium alloys and heat-strength cast magnesium alloys according to their use characteristics. Industrial casting magnesium alloys include binary and ternary alloys such as Mg-Al-Zn series, Mg-Zn-Zr series, Mg-Th series and Mg-RE series. Cast magnesium alloys are widely used in the aerospace industry. Due to its poor corrosion resistance, magnesium castings need anti-corrosion treatment before they can be used for a long time under atmospheric conditions.
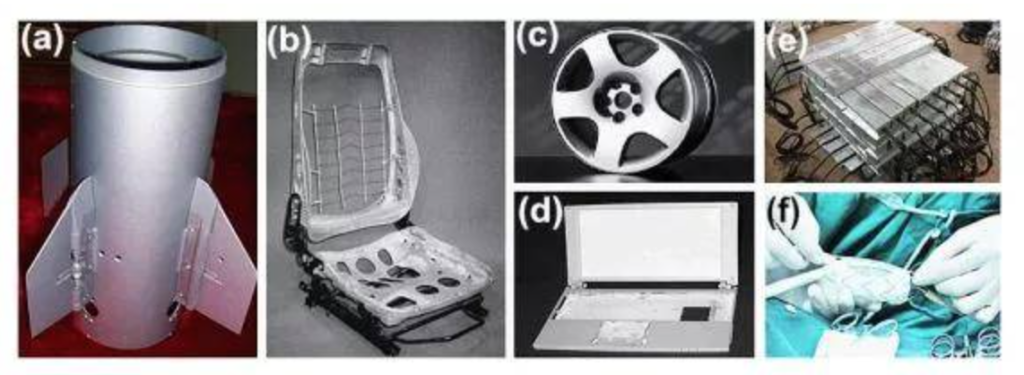
Alloy characteristics
- Magnesium alloy has low density but high strength and good rigidity
Among the existing engineering metals, the density of magnesium is the smallest, only 1.74 g/cm3, which is 1/5 of steel, 1/4 of zinc, and 2/3 of aluminum. Ordinary cast magnesium alloys have the same rigidity as cast aluminum alloys, so their specific strength is significantly higher than that of aluminum alloys. The stiffness of magnesium alloys increases with the increase of the thickness and the square ratio increases, so it is very beneficial to use magnesium alloys to manufacture integral components with good rigidity.
- Magnesium alloy has good toughness and strong vibration damping
Magnesium alloys are prone to large deformations when subjected to external forces. When subjected to an impact load, the energy absorbed is half that of aluminum, so it is very suitable for the impacted part-the wheel; magnesium alloy has a high damping capacity and is an ideal material for avoiding worker fatigue caused by vibration and noise.
- The heat capacity of magnesium alloy is low, the solidification speed is fast, and the die-casting performance is good
Magnesium alloy is a good die-casting material. It has good fluidity and rapid solidification rate, and can produce parts with fine surface and clear edges and corners, and can prevent excessive shrinkage to ensure dimensional tolerance. Due to the low heat capacity of magnesium alloy, compared with the production of the same aluminum alloy castings, its production efficiency is 40%~50% higher, and the castings have stable dimensions, high precision and good surface finish.
- Magnesium alloy has excellent machinability
Magnesium alloys are the easiest to machine of all commonly used metals. High cutting speed and cheap cutting tools can be used during processing, with fewer tool changes and low tool consumption. Another outstanding feature of magnesium alloy is that it does not require grinding and polishing, and a very smooth surface can be obtained with cutting fluid.
Risks in Machining Magnesium Alloys
Although magnesium material has many excellent properties, why are many people unwilling to process it? What are the reasons for this and what are the risks in machining?
While magnesium itself has a melting point of 650 degrees Celsius and is difficult to ignite, when turned into powder or shavings, the material becomes highly flammable, meaning chips made from machined magnesium could pose a fire safety hazard because it is difficult to ignite. Suppresses fires caused by magnesium, thus increasing the risk in the machine shop. Combustion will persist in nitrogen, carbon dioxide and water. This also explains why magnesium powder has been used in some explosive devices in the past.
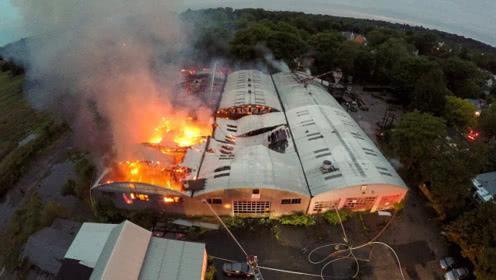
How to Safely Process Magnesium
- Avoid small clearance angles
Although magnesium can be machined quickly without compromising part quality, tight clearance angles are best avoided because contact between the tool and workpiece increases friction and cutting temperatures.
- Maintain proper tool condition
Sharp cutting tools reduce the fire hazard of machined magnesium. Dull tools rub and cause friction, which can cause sparks and build up heat where sensitive magnesium swarf forms. It goes without saying that sharper tools also produce better parts. Most machinists use carbide cutting tools with large relief angles to machine magnesium.
- Avoid using water-based coolants
Although coolants lower processing temperatures, water-based coolants generate hydrogen gas and therefore actually increase the risk of magnesium burns. Avoid coolant altogether, or use light mineral oil instead of standard coolant. Compressed air or argon can also be used to reduce temperatures without fueling a potential fire.
- Magnesium Parts and Chip Storage
It is extremely unlikely that the finished magnesium part will catch fire, but the swarf must be handled with care. Even after processing, magnesium can still be dangerous. Chips should always be kept dry, if possible, and stored separately from chips of other materials in an airtight container, such as a steel drum. Storage containers should be kept away from flammable materials. If the cuttings are wet, they should be stored in a remote location such as an outdoor storage shed.
- Prepare firefighting measures
Only used sand and a Type D fire extinguisher to extinguish fire.